How Construction is Keeping Supplies Moving During COVID-19
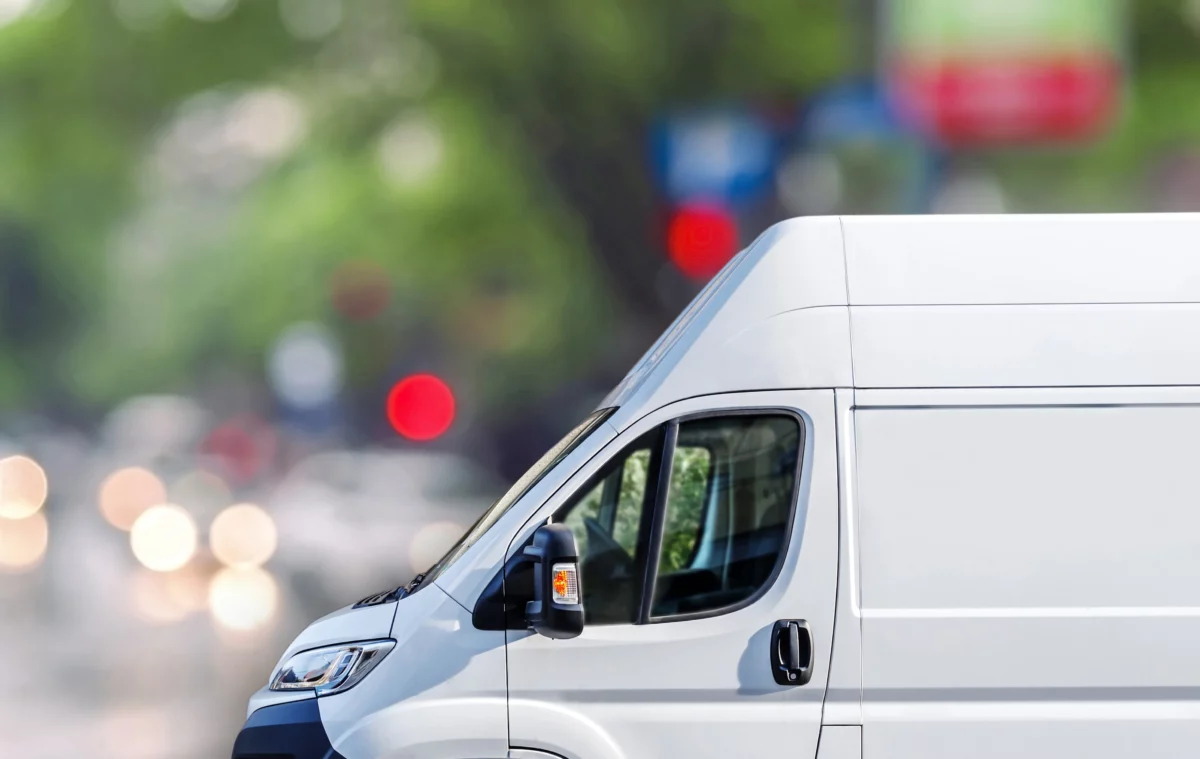
In just a few months COVID-19 has radically shifted the way we all do business. And it’s forced companies to adapt at speeds they wouldn’t normally.
It’s been a challenging time. But it’s also been encouraging to see the way businesses have stepped up to the plate.
In this post, we thought we’d look at some of the ways building suppliers have changed their operations to keep people safe and essential supplies moving.
Let’s get started.

1. Touchless Payment & Ecommerce
Many suppliers have reduced or eliminated cash and touch based payments to help avoid exposure to high touch objects.
Suppliers with ecommerce sites have also ramped up promotion of their online stores. This has helped raise awareness among customers who are used to popping into the store when they need something.
2. Promote Delivery Options
In many areas, suppliers have been mandated to close their showrooms or reduce their retail operations.
In response, suppliers have turned focus to their delivery services, including next-day, express, and same-day options. Some have even run ads focussed on the delivery timeframe, ease of ordering, and any costs associated with the service.
TIP: Not set up for delivery? Apps like GoFor can help. Start offering delivery today — learn more.
3. Offer Curbside Pickup
In addition to delivery, many suppliers are offering curbside pickup. Many have created clearly marked outdoor drive-through areas for customers to receive orders.
Businesses are preparing orders in advance, then asking customers to call or text when they arrive. Orders can then be placed outside, or directly into the customer’s vehicle while maintaining social distance.
TIP: Make sure you communicate instructions to customers when they place an order, and the pickup area is clearly marked to reduce confusion.
4. Prepare Paperwork in Advance
Another way suppliers are reducing contact between customers and staff is by ensuring orders are prepaid and paperwork is clearly attached to the order.
Some suppliers have introduced digital paperwork and signatures, as a way of keeping records up-to-date without requiring staff and customers to touch paperwork. Others have simply eliminated the need for signatures on delivery.
TIP: Apps like GoFor make switching to paperless delivery simple, with photo confirmations and digital delivery notifications.
5. Communicate Safety Procedures
Safety guidelines and community regulations are changing constantly. We’ve seen suppliers communicate their safety procedures in a variety of different ways — from social posts to bristol board signs.
TIP: It’s a good idea to promote your delivery options and safety procedures across as many different channels as possible to reach the broadest audience. Some examples are:
- Social media
- Email updates
- Website banners
- Store signage (window signs, sandwich board signs, etc)
6. Mandate and Provide Personal Protective Equipment (PPE)
Suppliers have taken a variety of steps to ensure the safety of staff and customers. Many have provided access to hand sanitizer, increased store cleaning frequency, and provided staff with PPE (such as gloves and masks).
TIP: Regularly check and follow safety guidelines from health professionals:
- https://www.canada.ca/en/public-health/services/diseases/2019-novel-coronavirus-infection.html
- https://www.who.int/emergencies/diseases/novel-coronavirus-2019/advice-for-public
- https://www.cdc.gov/coronavirus/2019-ncov/index.html
7. Maintain Social Distance
Another way suppliers are ensuring the safety of their staff is by reducing distance and social interaction in stores and on delivery loading/unloading (6 to 10 feet).
Some have even created visual cues, such as chalk or tape lines, to help maintain social distancing.
TIP: Don’t forget to communicate policies with your delivery drivers! Include any safety procedures in the notes on your delivery.
The Bottom Line
Business operations may have changed drastically in the last few months, but many suppliers have stepped up to the challenge. They’ve introduced new safety procedures to keep customers and staff safe. And many have ramped up delivery services to keep supplies moving in a timely manner while ensuring their customers’ projects stay operational.
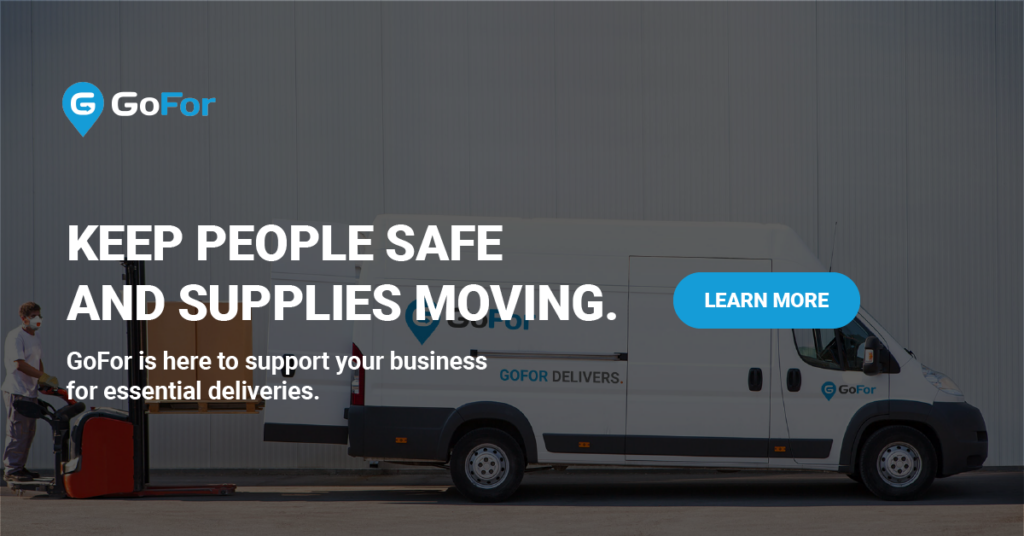