4 Ways Data Can Inform Logistics Optimization
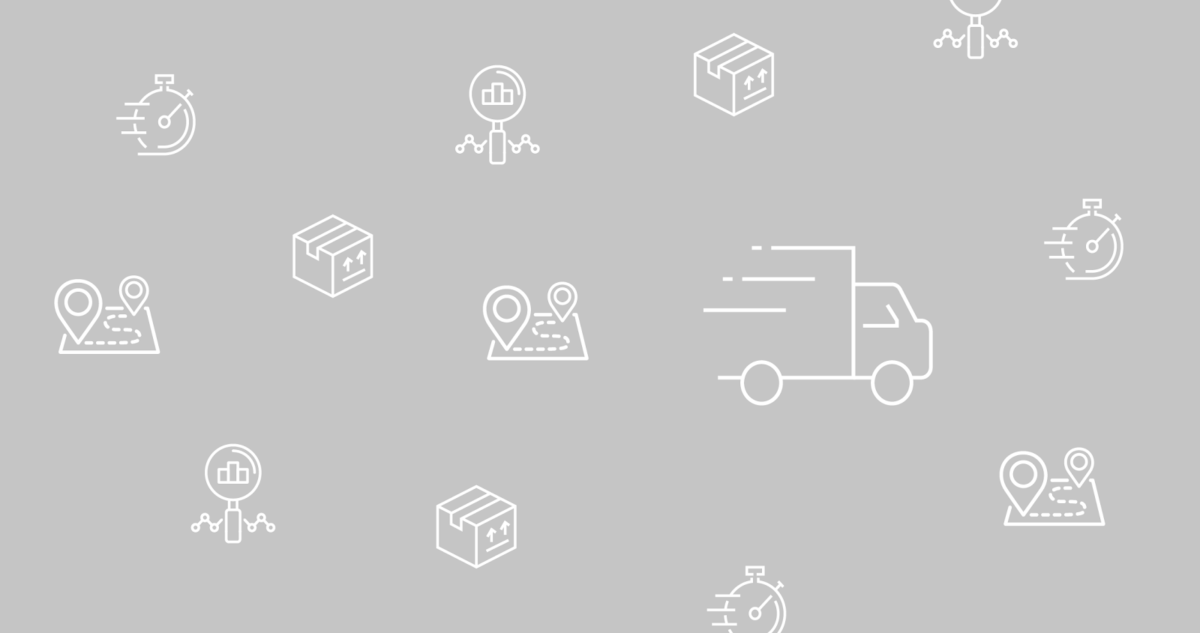
The world is going through a digital transformation right now — and as processes move from paper to the cloud, one of the benefits is an influx in data.
Logistics is no exception.
Your supply chain creates an immense amount of data on a daily basis. And you can use this information to inform your supply chain optimization techniques.
In particular, data can shine a light on traditionally difficult to measure parts of your supply chain — like the last mile.
In this article we’re going to look at how data can inform both strategic optimization and tactical optimization of your last mile approach.
Let’s get started.
Strategic Optimization
The expectation for same-day (even 3 hour delivery) is rising. Fast, reliable delivery should be part of every company’s brand strategy objectives if they want to stay competitive.
Achieving fast, reliable delivery requires transparency — both across your organization and with the end-customer.
Logistics data can create alignment between marketing and the supply chain. It can inform the days, times, vehicles, and service levels you offer to ensure you get the best costs. And it can help manage customer expectations — leading to better delivery experiences.
1. Create transparency with Real-Time Delivery Tracking
Real-time tracking has become the new standard for deliveries. Yet 73% of supply chain professionals can’t currently provide real-time tracking to customers.1
Real-time delivery ETAs help manage customer expectations, leading to a better delivery experience. Even when delays inevitably happen, keeping customers updated on the status of their delivery helps to reduce frustration.
Modern logistics platforms combine GPS tracking, algorithms, and automated processes to create transparency at every stage of the last mile process. This technology also enables more in-depth reporting, providing greater predictability for logistics professionals.
2. Inform Delivery Offering
Using data to inform your service level promise helps align customer expectations with delivery realities, leading to happier customers.
When marketing knows your capabilities on delivery turn time they can communicate with confidence. Instead of starting with a marketing promise and putting pressure on the supply chain to fulfill, you can look at the data to see what you can actually achieve.
This lets you identify ahead of time if you’ll be able to deliver on your promised service levels. If you can’t, you can take steps to quicken the delivery process — before you upset customers.
TACTICAL OPTIMIZATION
In addition to informing your customer strategy, logistics data is also useful for optimizing the execution of your delivery programs.
Modern logistics platforms collect otherwise siloed supply chain data in one place. You can then apply technology like AI and machine learning to find efficiencies at scale.
4. Optimize your delivery routes
The route a driver takes can have a significant impact on the time and cost of your delivery. But manually optimizing routes can be challenging. There are a ton of factors to consider — from driver availability to traffic, delivery windows, and vehicle capacity.
That’s where big data comes in.
Using your supply chain data, auto-dispatch technology can automatically generate an optimal route. Algorithms optimize routes based on a variety of business rules and detailed constraints.
This helps reduce delays and ensure drivers make the most efficient trip possible. With the right supply and demand, we see reductions of empty miles in the range of 30-40%.2
5. Pinpoint controllable delays
Route optimization plays a huge role in navigating traffic congestion and delays. But it’s only part of the picture.
Many factors can affect delivery speed — such as pickup and drop-off congestion, time of day surges, and delivery distance. Modern logistics platforms can highlight deviations in the data that help you pinpoint these delays in real-time.
This lets you see exactly where delays are happening, and immediately take action.
The Bottom Line
As customer expectations for delivery rise, organizations need to make smarter, data-backed decisions about their delivery strategy and execution.
Logistics data can help you pinpoint delays, optimize your routes, define predictable service levels, inform your customer strategy, and create transparency with end-customers.
But it’s important to remember identifying these issues is only the first step. Organizations will also need to consider their supply chain agility, and partner with logistics companies that can help them realize the efficiencies their data highlights.